Small and medium sized enterprises (SME) need information of production processes, machine load and maintenance processes for an efficient and optimized resource planning. Specialized systems, e.g. for capturing of production data and machine data as well as systems for capturing of labour time are used within big enterprises for those purposes. Such a variety of systems may not be economically used within SMEs. Therefore more compact methods and solutions will be developed within the project autoAPSint, which enable SMEs to use on-line information from the automation and control levels of the production equipment for an efficient and optimized resource planning. The solution will be characterized by a less complex IT infrastructure to be used for Advanced Planning and Scheduling (APS). It will be designed to be easily administrated spanning over all departments of the enterprise. That solution will be characterized by a high degree of automation for activities like data integration and configuration.
Partner
Projekt leadership
ism GmbH
Further project partners
ifak system GmbH (now THORSIS Technologies)
ifak e.V.
Downloads
At this page you will find some XML schema files. The are used within the autoAPSint project for the data exchange between production management staff and technicians (electrical engineers or maintenance staff).
KPICatalog.xsd: This schema defines the structure of catalogs containing definitions of so called Key Performance Indicators (KPI). Those KPI are for example 'Load factor of machinery', 'Quantity in pieces' or 'Plant availability'.
AggFunctionCatalog.xsd: This schema defines the structure of catalogs containing definitions of aggregation functions. Those functions are for example 'Maximum value', 'Minimum value' or 'Mean value'.
ApsConfiguration.xsd: This schema defines the structure of a configuration file for a data acquisition system. It references KPIs and aggregation functions of the relevant catalogs, which additionally are combined with scheduling for the data acquisition sampling of on-line data values. All KPIs are related to resources, which already are managed within the ERP system. Alarms and writable values may additionally be defined and related to the resources.
A scientific article about the projekt you may find on-line: FORMALIZED ENGINEERING OF THE INFORMATION EXCHANGE BETWEEN AUTOMATION AND PLANNING SYSTEMS.
Contact
isM
integral systemtechnik GmbH
Barleben site
Steinfeldstraße 4
39179 Barleben
Tel: +49 39203 966-0
Fax: +49 39203 966-77
Email: info@isMsystem.de
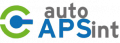